Tidewater Turnaround: How the Prince George Refinery Achieved All Time, Schedule & Safety Objectives
- All turnaround objectives met: time, schedule and safety.
- Significant hard savings in cost management labor.
- External workforce optimization: hours increased 20% based on data-driven insights to meet schedule.
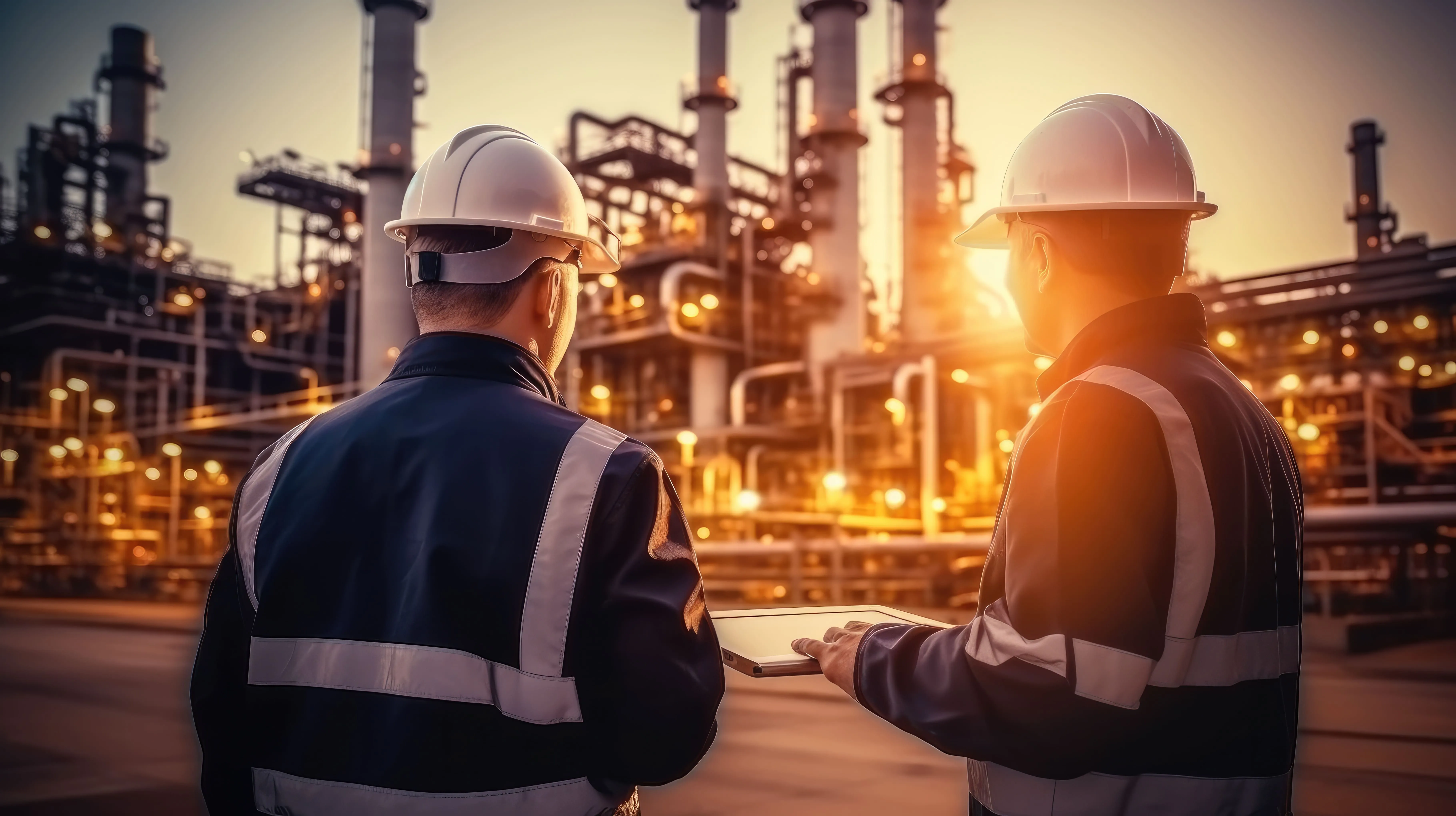
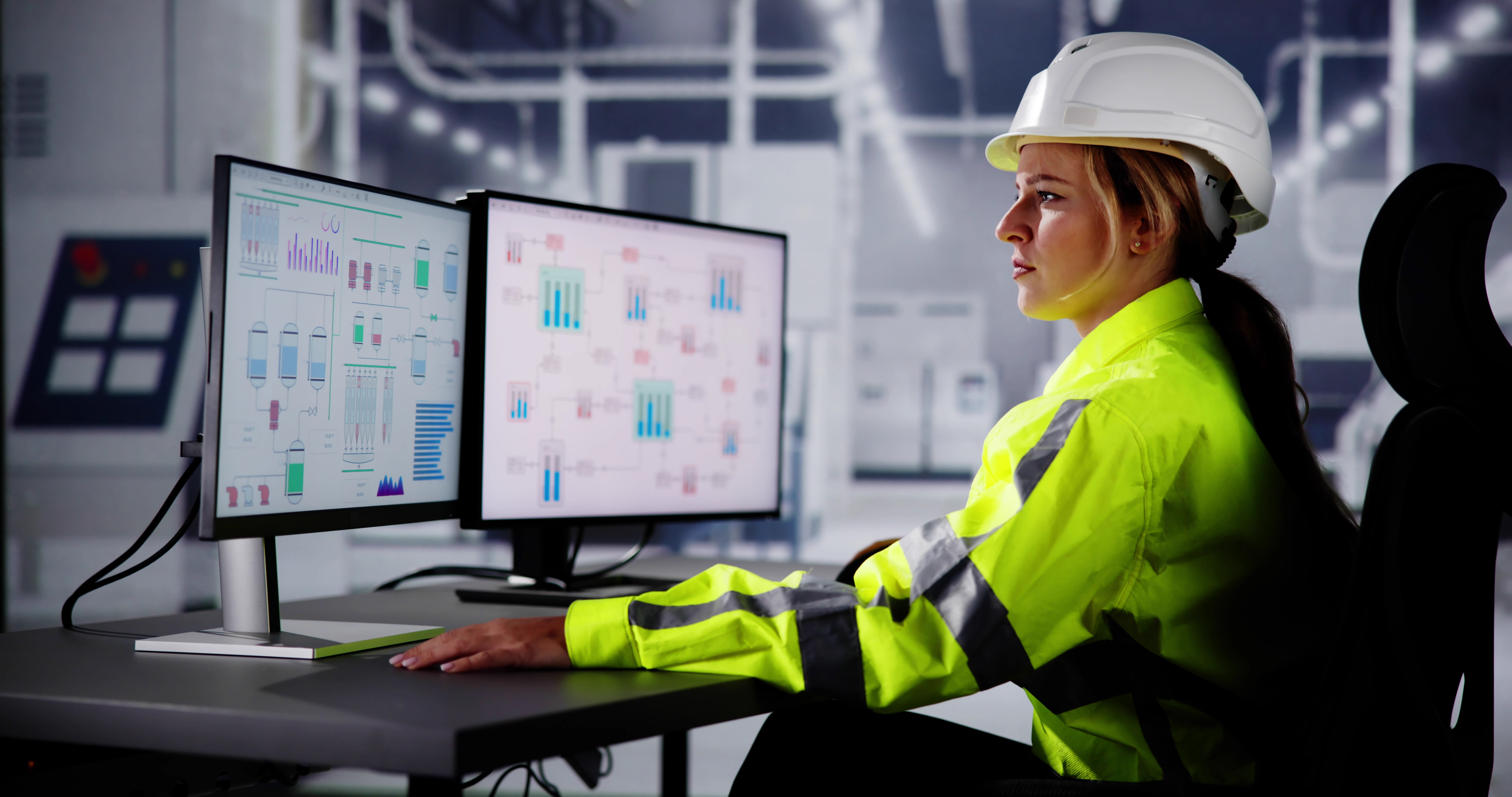
To complete a recent turnaround, the Tidewater team scaled up its workforce from 30 contractors to 600 across 10 vendors with their own contracts, schedules and relationships to manage. Erik Sullivan, Turnaround Manager at Tidewater, identified the top three challenges:
- Verifying manual pay-per-time tickets to support project planning and cost and risk avoidance in a timely manner.
- Reconciling the details of every contract, to reduce discrepancies and overspending.
- Avoiding spending overlaps with contractors shared between the turnaround and a large green capital project running simultaneously.
The solution
PayShepherd turns labor, equipment, materials, and subcontractor (LEMS) data into insights, helping identify trends and issues. The Tidewater team chose PayShepherd to transform time-intensive, Microsoft Excel-based processes into streamlined digital LEMS verification and reporting to empower real-time cost transparency and contract compliance visibility.
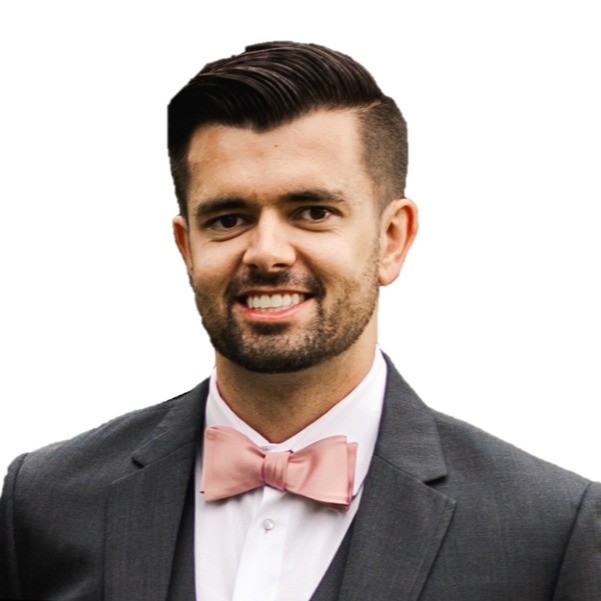
“PayShepherd eliminates the big problem of ensuring all contractual rates are checked. The PayShepherd daily proforma invoice, backed by its 50+ controls and checks, gives me confidence that contractors were on site for the time invoiced and didn’t violate any rules we set up. I can now approve invoices safely, knowing that all contractual rates and agreements are met.”