Is a lump sum contracting strategy really less risky?
What are the decisions you consider when selecting your projects contracting strategy?
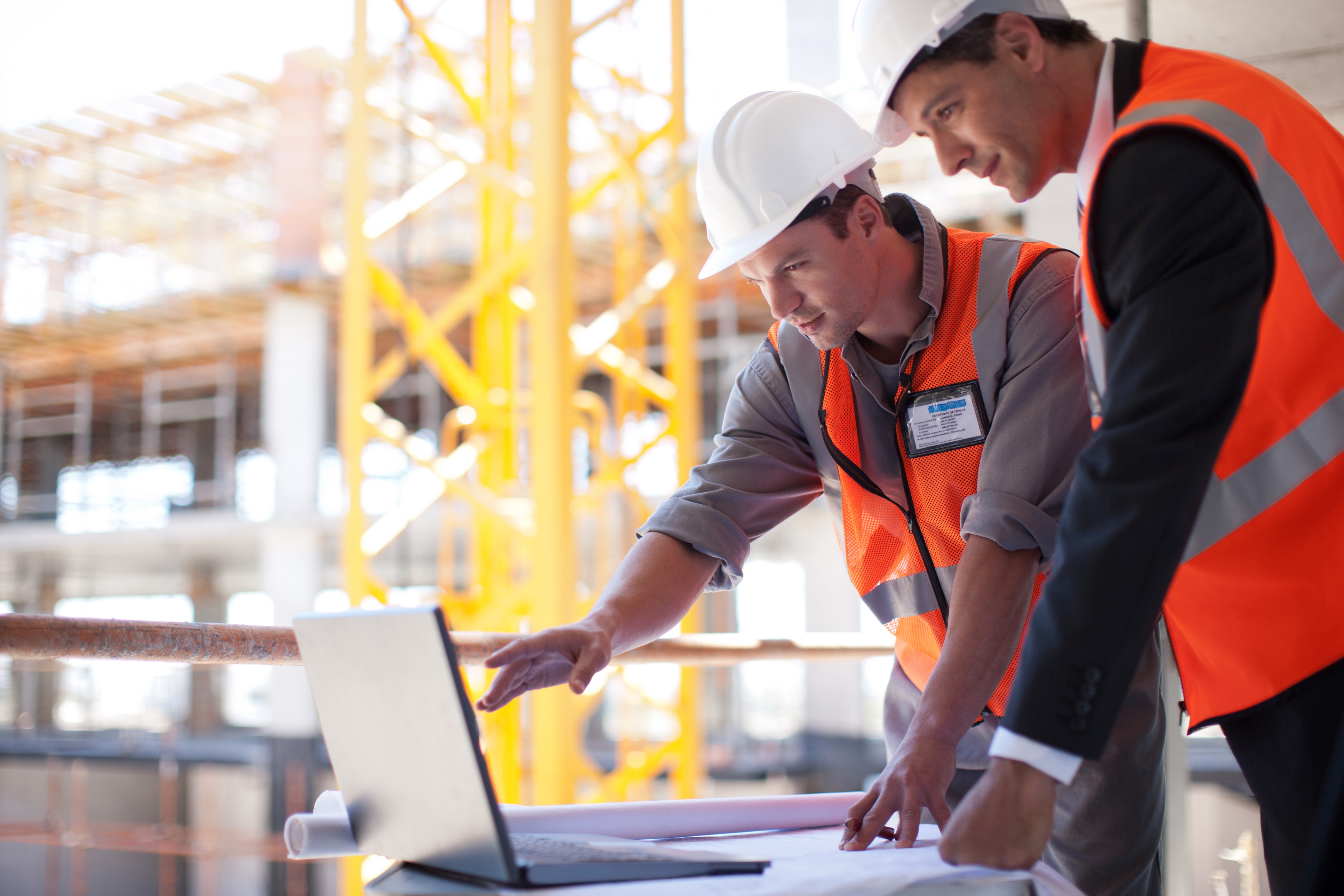
Call it what fits best: Fixed Price, Lump Sum, EPC (Engineering, Procurement and Construction) or LSTK (Lump Sum Turn Key) projects.
All of these are a form of contracting arrangement used, among others, in large infrastructure, power plants, oil and gas, or mining, where the contractor is responsible for all activities. These include everything from design (in some cases), to procurement, construction, commissioning and handover of the deliverables to the owner or operator.
These projects are typically large and complex. More than half of them at $1 billion or more around the world suffer from large cost overruns and major delays.
What are the reasons for overspending? Is there a way to prevent it?
Take a closer look at a few examples.
Site C (B.C., Canada)
Site C hydroelectric dam on the Peace River is an example of a megaproject where the cost almost doubled compared to the initial estimate. The Site C feasibility study in 2007 assumed an initial budget of $6.6 billion. The cost projection was updated in 2011 to $7.9 billion and revised in 2014 to $8.3 billion when construction on the project started. Since then, the project struggled with several difficulties, including a tension crack that appeared on the north bank during slope excavation and stabilization activities (Site C Project). As a result, the 2019 river diversion timeline was missed, while direct and indirect construction costs increased. The final budget is currently estimated at $10.7 billion with more than $1.5 billion to address potential risks to project costs.
Plant Vogtle (GA, U.S.)
The two-unit Plant Vogtle nuclear power station is expected to begin operating in 2021 and 2022, respectively, which is about five years behind schedule and more than $13 billion above budget initially set up at $14.3 billion. Problems include issues with construction, paperwork and contractors, which were changed several times. In 2009 the construction was delayed by at least six months due to the lack of regulatory approval for the backfill, used to fill the excavated area, after 3.6 million cubic yards of dirt were removed at the site in preparation for construction. After the project contractors were forced to repair “welds on [reactor components] that were found to be the wrong type of weld” in 2012, the project was a full year behind schedule. An additional eight months of delay was caused by problems with the paperwork needed to move a prefabricated section of the plant from a factory in Lake Charles, La.
Grande Prairie Hospital (AB, Canada)
Another example of a project which has run over budget and schedule is Grande Prairie Hospital. The original contract dated back to 2011 and assumed a budget of $319 million with planned project completion in 2015. The cost has since escalated to $763 million and the hospital is still under construction due to “poor planning and continual scope changes that led to added costs and delays." According to Graham Construction, the original contractor, the project has been subject to more than 600 change orders and more than 400 design clarifications, and many of them “required demolition of completed work to accommodate the new scope.”
Megaprojects are characterized by technical and organizational complexity and there are many factors that cause project failure. These factors are hopefully identified and laid out in the design and development stage, prior to the final investment decision.
What are the decisions you consider when selecting your projects contracting strategy?
We can help! Let's talk.