The costs hiding in contractor timesheet processes and what you need to know
How manual processes contribute to cost leakage and other headaches
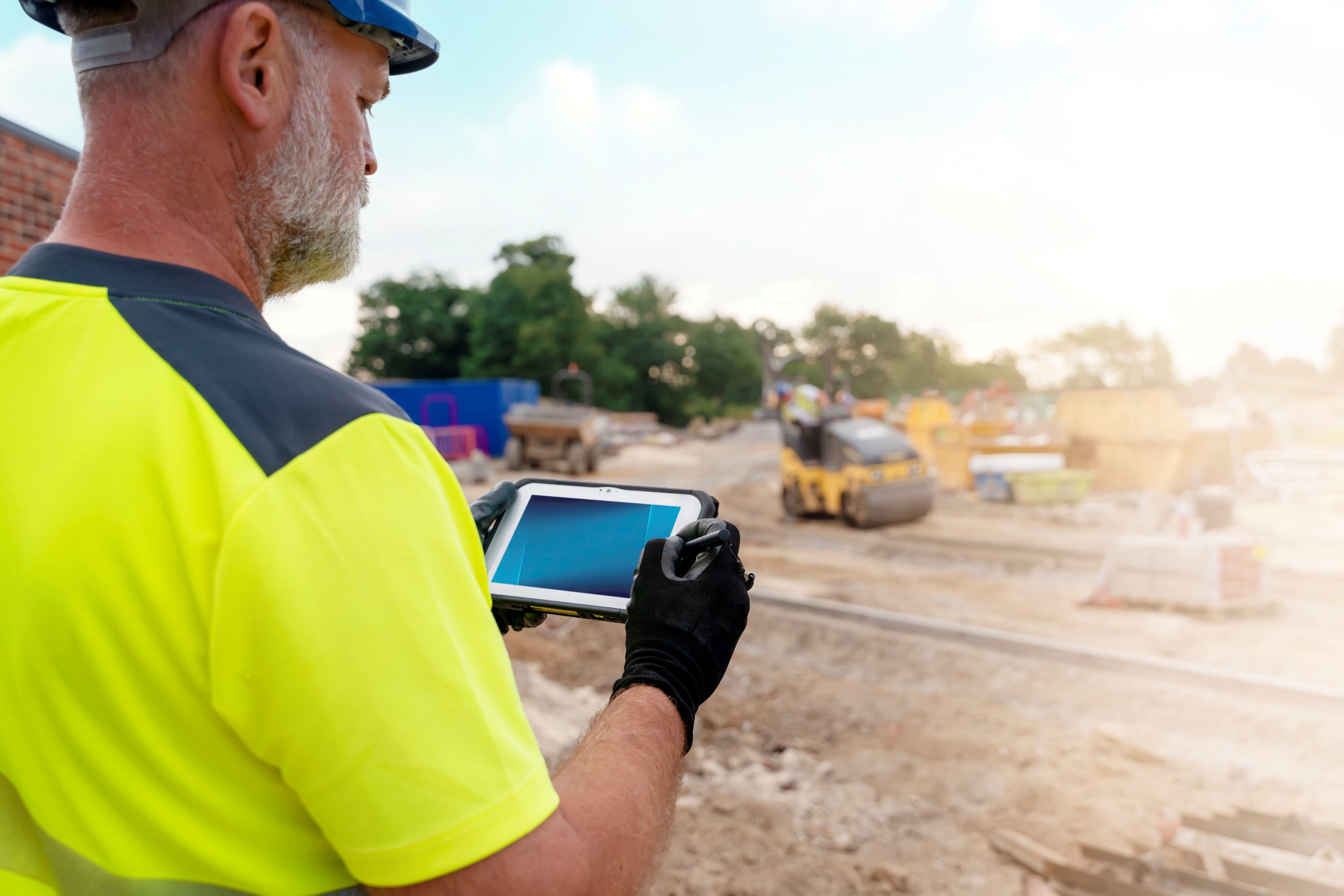
The financial health of your projects is vital to continued success and completion, and contractor timesheets give you a snapshot of that health at any given time.
And like any good checkup, taking a closer look at your contractor timesheets can help you spot potential concerns early so they don’t become a major problem further down the line.
Chief among those concerns? Cost leakage. In a time where every dollar counts, hidden costs and expenses that add up quickly can’t be ignored.
The root cause behind all this? Manual processes. The human element means mundane errors can slip through the cracks, causing your business to spend more than it should be.
Good news, though: there is a solution.
In this blog, we’ll explore:
- The problem with manual timesheet processes
- What costs could be hidden in your contractor timesheets
- How automating timesheet management can help
Let’s dig in!
The problem with manual timesheet processes
Manual timesheet processes are, to put it lightly, tedious and time consuming. Think about it: every single element on a contractor timesheet and submission needs to be carefully compared to contract terms to ensure compliance.
Traditionally, most supply chain tasks have relied on manual intervention to get the job done. As other elements of the supply chain are increasingly digitized, the fact that these reviews are so often reliant on pen-and-paper processes sticks out.
The chief problem this causes? Manual timesheet processes increase the likelihood of errors slipping by unnoticed.
That’s not a critique of staff assigned to these tasks, it’s just a fact: the error rate for manual data entry and review can range anywhere from 1 to 5%.
And even small errors on contractor timesheets can cause problems. They add up over time, compounding into serious cost leakage. Subtle mistakes in labor rates, inaccurately logged work hours, discrepancies in travel and equipment charges… it all eats into your budget.
What’s more, these problems have far-reaching impacts. Think of a snowball rolling down a hill and picking up speed, growing in size; it’s not a big deal now, but it will be later on.
As an example, manual rounding errors add up to extra time, which then leads to project managers allocating more resources. One slightly inflated estimate suddenly means a delayed start for subsequent tasks, forcing teams to adjust their schedules.
And perhaps worst of all, error-prone manual processes require investigation and follow-up, which in turn can leave your contractors feeling scrutinized. This can, in moments, undermine all the good will built between you and your contractors, potentially causing irreparable damage to the relationship.
The hidden costs in contractor timesheets
So manual timesheet processes cause problems and can incur hidden costs—but what exactly are those hidden costs?
Most of these costs will fall within one of five categories:
- Incorrect labor rates
- Non-compliant labor hours
- Travel expense discrepancies
- Non-compliant equipment expenses
- Unapproved material costs
Let’s take a quick look at each one.
Incorrect labor rates
When you hire contractors to work on your projects, you agree upon specific labor rates for the workers on the job. A standard laborer might get an $80 an hour rate while an electrician gets $90 an hour.
You also agree upon worker classifications and premium rates; apprentices aren’t paid the same as more experienced workers, and overtime rates are set ahead of time. Timesheets that don’t accurately reflect all these details can rapidly add up to massive overpayments and billing issues, not reflecting the actual value of the work.
This isn’t necessarily malicious—fraud does occur, but it’s just as likely that typos and miscommunication are the root cause of these all-too-common headaches.
Accurately checking and verifying these rates means manually sifting through reams of data. That’s a huge ask for someone just trying to sign off on contractor timesheets, especially when their time could be better spent pursuing more strategic initiatives.
Non-compliant labor hours
If you spent two hours and fifty minutes finishing a task, and someone asked you how long it took, would you say two hours and fifty minutes, or would you round up to the full three hours? It’s a pretty minor difference at the end of the day, right?
Well, yes and no.
Timecard rounding is a fairly standard practice in many contracts and among many employers—generally speaking, time worked might get rounded up in increments of five, six, or fifteen minutes, depending on the contract.
But how rigorously is that enforced when a contractor is reporting their own time, and how do you track it accurately?
If contractors consistently round up beyond agreed-upon limits or standards, pretty soon you’ll be stuck dealing with massive overages. This has a compounding effect on your project’s overall health, too. Suddenly, cost estimates are distorted due to these non-compliant hours, and you’re stuck trying to allocate even more resources than initially planned.
That’s not the only risk, though. Workers consistently logging time beyond previously established budget hours can introduce major legal risks. If contracted employees were to continuously log overtime hours or additional work hours, you might be on the hook for violating labor laws or union agreements.
In other words, you need to be tracking a lot of shift scheduling information to keep tabs on what’s going on on the job site to avoid these all-too-common hidden costs.
Travel expense discrepancies
Per diems, living out allowances (LOAs), and travel expenses are par for the course in contracts everywhere.
Yet these common expenses are also fertile ground for discrepancies and overages. Excessive claims, unapproved travel arrangements, and per diem claims exceeding established limits are some of the most common issues found lurking in contractor timesheets.
The problem, as always, is spotting them.
Unless your staff handling contract compliance are manually reviewing commute times on contractor timesheets themselves, then you don’t necessarily have complete visibility into what’s going on with these expenses.
Things to watch for include:
- Logged commutes that are longer than actual travel distances
- Accommodations outside designated locations
- Exceeded meal and lodging limits
Non-compliant equipment expenses and usage
The equipment your contractors use is also a potential minefield of hidden costs. These errors most commonly occur when invoiced operating time doesn’t match the work being done on site—in turn making it harder to accurately budget for the job at hand.
These are easy-to-overlook details that require a careful cross-examination of contractor timesheets.
In some cases, this is an incredibly easy discrepancy to spot, given that only certain contractors may operate certain pieces of equipment. If an equipment is logged as running for 10 hours, but the operator was only on-site for 8 hours, then obviously there’s an error that needs to be addressed.
In other cases, equipment might be listed as running non-stop… despite records and schedules showing planned shutdowns or maintenance.
Regardless of how it manifests, both issues typically stem from manual timesheet entry and inaccurate time tracking. Both lead to cost overruns if they’re not caught in the timesheet submission.
Unapproved material costs
During your contracting processes, you would typically agree to expenses and cost estimates around the materials used for the job—and sometimes, those costs rise due to increased need.
These increases are usually reflected in purchase orders and change orders, leaving a useful paper trail to help project managers review what happened, why, and when.
But sometimes contractors list additional fees for unapproved tools and materials, separate from the overall labor cost.
In other instances, cost leakage occurs from overpriced supply costs and excessive markups. Like all the hidden fees we’ve discussed so far, these add up over time and make it harder to accurately manage a project and its budget.
The best way to prevent these hidden costs is with regular review and auditing of your budgets. You need to make sure you’ve got complete insight into what’s going on on your job sites and what’s being logged in contractor timesheets.
How to leverage automation for timesheet management
By now, one theme should be apparent: manual timesheet processes are a problem for everyone involved.
Your contractors hate feeling like every step they take is carefully scrutinized.
Your procurement team is stuck manually reviewing contract compliance, carefully checking (and double-checking, and triple-checking) terms and conditions.
And at the end of the day, your business is leaking costs because it lacks accurate insight into what might be lurking in run-of-the-mill timesheets.
If that sounds like a lot, that’s because it is. For as much innovation as you found in contractor-heavy industries, legacy tools and manual processes still dominate many of these.
Good news, though—automating these tasks gives you a way to put an end to hidden costs while putting a plug in cost leakage.