3 Ways to Rise Above Manufacturing’s Labor Shortage in 2023
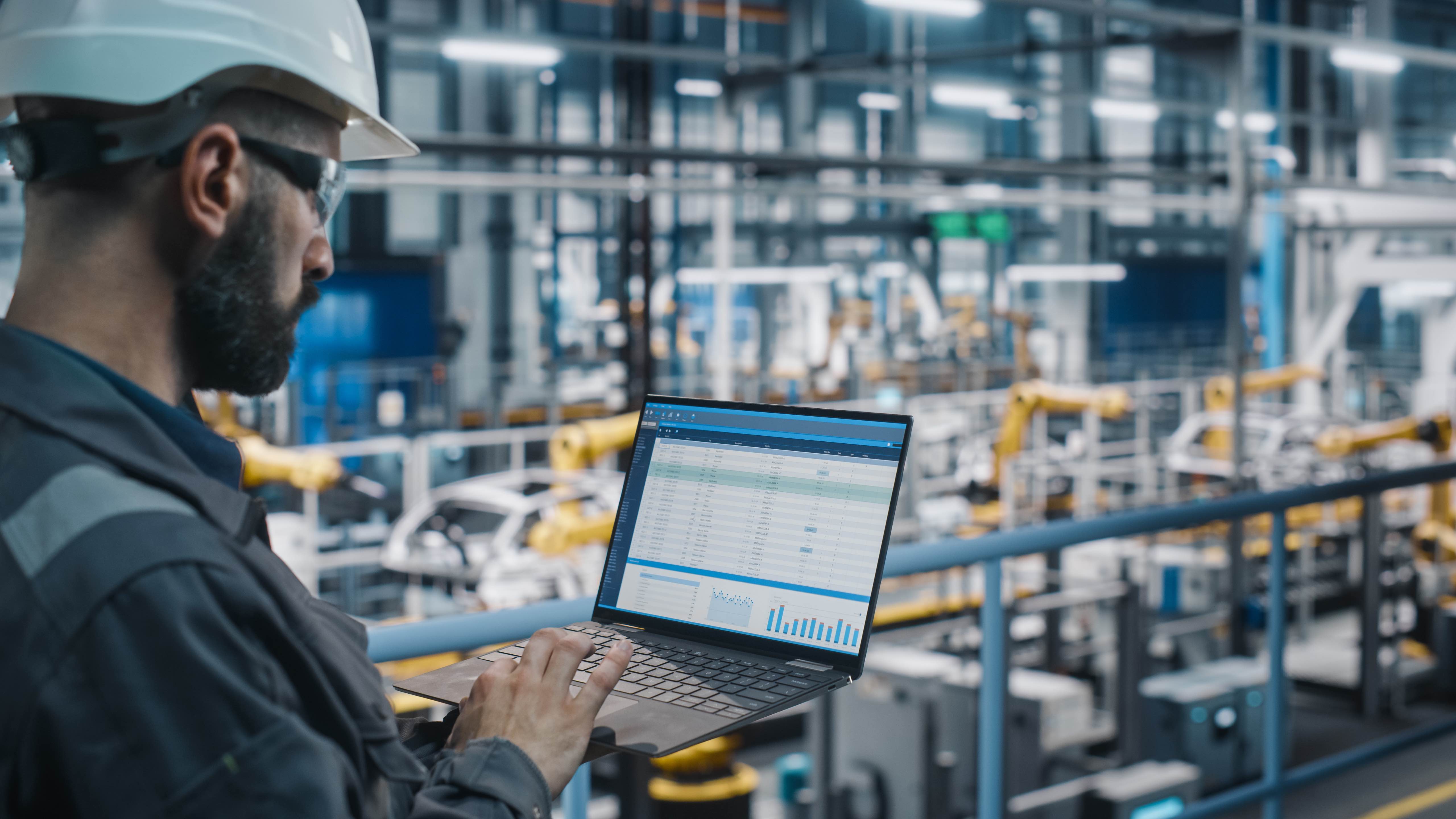
Focus on what you can control
Reading about labor shortages in the news is one thing. When it directly affects your bottom line, it’s another.
In the last couple of years, Canadian Manufacturers & Exporters (CME) findings show over 80% of manufacturers have faced immediate labor shortages. That’s an increase of nearly 40% since 2016. Even worse, nearly half of North American manufacturers have either lost opportunities or paid penalties as a result of their inability to attract enough workers to meet their production goals.
For the first time in years, there are more job opportunities than there are applicants to fill them, especially in general labor and skilled trades positions. According to the U.S. Chamber of Commerce, even if every skilled worker in the country were employed, the manufacturing industry would still be short approximately 35% in workforce despite high levels of unemployment.
It’s a tough pill to swallow, to be sure. And, it’s not going away anytime soon. By 2030, a recent Deloitte report estimates the U.S. may fall short on manufacturing workers in excess of 2 million people, especially as baby boomers, many with different experience, workplace attitudes and values, retire.
Things are not looking any better for our European friends in the industry. According to Deloitte, manufacturers in the U.K. are dealing with job vacancies 30% higher over just the last couple years, the worst skilled labor shortage they’ve faced in over 3 decades. It’s expected Europe will lose 13.5 million workers, 4 million in Germany alone, by 2030, according to a McKinsey study.
It’s a problem estimated to cost the industry trillions of dollars every year for the next decade.
Industry experts have identified three key ways to address the labor shortage. The first two, immigration and attracting under-represented groups, depend heavily upon government programming, so are situated less within the industry’s control. But the third solution–adopting Artificial Intelligence (AI), Intelligent Automation (IA), and new technologies–is fully within an organization’s control and can make a deep impact, fast.
Here, a rundown on the top three answers to the labor shortage problem.
Boost economic class immigration.
In North America, filling labor shortages in manufacturing is heavily dependent upon immigration. Bringing in more economic class immigrants is essential to supplementing the existing workforce on both the executive professional side and in skilled labor scarcity. Across the pond, it’s large-scale emigration further East or West that’s exacerbating the problem.
CME recommends doubling the country’s economic class immigration target in recognition that this group of people is driving Canada’s labor force. To support this initiative, it’s also recommended the federal government broaden the definition of “economic class” to include a wider range of candidates, and that manufacturers help out by providing programs, such as language training or mentorship provision.
South of the border, U.S. Chamber of Commerce findings indicate only half as many qualified workers are available to fill all the job opportunities within the sector. And, the trend continues to grow worse. Industry members are calling on congressional leaders to bring in more immigrant workers, a more immediate fix, and to promote STEM education, a longer-term solution competing nations, like China, are already investing in.
Attract underrepresented groups, including youth.
There’s no denying manufacturing in North America has been a traditionally male-dominated industry. That trend eliminates nearly half of the potential labor force as 48% of women contribute in general, but less than 30% in manufacturing, according to Statistics Canada and the U.S. Department of Commerce. These numbers have essentially stalled for over 3 decades. Not only would attracting more women to manufacturing help companies grow and replace an aging workforce, it would offer women fulfilling skilled careers that are high paying.
Also critical is attracting more youth to the industry as that demographic currently sits 3 times lower than 1976 numbers, according to Statistics Canada, and again, all those baby boomers are retiring off. Attracting, but also retaining, more youth in the manufacturing workforce is one of the top-listed answers to labor challenges around the world.
Again here, promotion of STEM education plays a central role. It’s also important that companies create a safe and respectful workplace environment for all age groups and gender identities that is diverse, equitable, and inclusive. Prioritizing this pays back big time. Research shows inclusive and diverse teams make better decisions nearly 90% of the time, driving profitability and long-term employee retention, not to mention a much larger talent pool from which to draw the best person for the job.
As part of the answer, industry experts suggest lessening labor market exits by improving job match services and addressing skills mismatches. Additionally, a commitment to fostering work-life balance is critical to attracting new demographics to the workforce as people’s values have evolved over the years.
Invest in automation & technology.
If there’s a silver lining to be appreciated in these challenges, it’s the fact that the door is wide open to deploying advanced artificial intelligence and automated innovations that improve performance, productivity, and job satisfaction. Just think, that younger demographic that facilities are trying to attract, and keep, has grown up with mobile devices in their hands since they can remember.
Investing into automation and other advanced technologies is the most immediate solution manufacturers can turn to in order to combat labor shortages and remain competitive in their production. In fact, countries with less capital investment into technology are quickly being left in the dust as other nations ramp up their production and competitive edge by understanding and embracing the latest advances.
Effective solutions are extending the human capacity to increase productivity, safety, profitability, satisfaction, and quality. In handling the minutiae of time-consuming manual tasks, these technologies free up peoples’ minds for bigger picture, more strategic, rewarding, and proactive thinking.
The best advances are purpose-designed to alleviate the typical hesitations around adopting new systems.
Cost. Ideal solutions should prove a valuable ROI on their implementation and deployment.
Increased productivity. Beyond the ROI, these systems will make way for more efficient processes that help humans focus on high-value work.
Worker value. The best innovations are designed with the user in mind and are built to simplify, improve, and empower them in their daily lives, not complicate them.
Above & beyond service. Automated solutions should be human-centric, not tech-centric. The best providers employ people who truly understand and care about the people using their systems.
Continuous improvement. By being data-driven, better decisions are made and easily backed with hard proof. Constant improvement, including strengthened relationships, becomes the norm.
Manufacturers who embrace the AI & IA revolution will be better poised to remain competitive than those resisting the movement. There’s no getting around the challenges incited by the labor shortage, but there are effective solutions available to mitigate its effects. While immigration and greater diversity hold the potential to lessen the critical nature of the problem, they depend on government programming, and we all know that takes time.
But, seizing the opportunities held in the automated movement is an immediate solution that’s fully within the control of facility management.
It’s not a question of risking jobs by replacement. The best IA solutions will scale human capacity, keep operations and processes running smoothly, and at the end of the day, keep people employed at successful businesses.
There’s only so much we can control when it comes to manufacturing’s labor shortage. So, when incredible opportunity presents itself and it’s easily and quickly implemented, why risk being left behind? Make 2023 the year you future-proof your business by embracing the power of automation and advanced technology.
Not sure where to get started? We get it, and we’re here for you. Our solution is the ultimate fusion of the best in IA & people who truly know the manufacturing industry. Let’s talk!