How PayShepherd supports plant maintenance and engineering managers
Transforming superhuman expectations into superhuman results
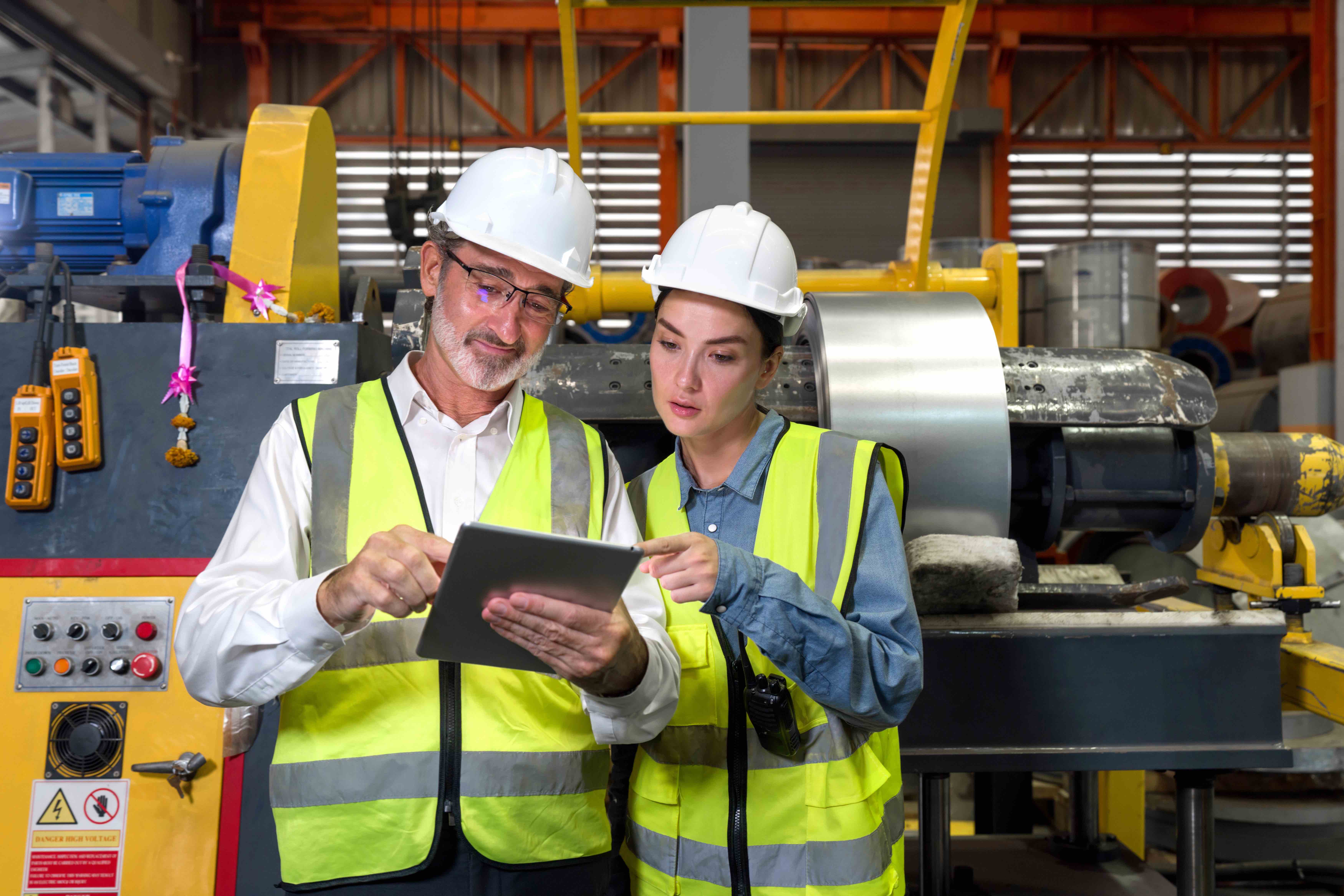
There’s a significant administrative burden on engineering and maintenance managers working on cost reimbursable (i.e., time and materials) projects with operations, maintenance, and capital projects contractors. Work orders, daily bids, purchase orders (PO), daily force account sheets, site access, invoice reviews — all these are manual and time consuming tasks without having software built to understand and manage them.
These managers spend a lot of time trying to understand what the contractor is doing and why they’re doing it, as that’s ultimately what they’re billing for. Since it’s the mill’s equipment, there’s also the interface with the operations team that needs to be managed. And accounting is always asking managers for the cost to complete accruals and when POs can be closed out. While they want to give the right answers, it often feels like a crystal ball is the only tool available.
While mills want to take a proactive approach to adjusting scope, managing crew mix and labour loading, and sequences of events that influence the cost of work, it’s often seen as idealistic because there’s so much going on that the default mode is always reactive.
Why is plant management so difficult?
There are a number of key responsibilities that come with being a maintenance and engineering manager:
- Contract administration where there’s hundreds of validation points to ensure validity of costs
- Overall management of contractors and their interface with operations
- Multiple needs and demands from accounting, finance, and mill management
They also act as area superintendents, managing safety compliance, QA/QC, technical issues, and maintaining the facility’s schedule of the work.
It can feel like a superhuman expectation, fitting 100 hours worth of work into one day. The reality is that managers do what they can in this incredibly taxing environment.
How PayShepherd helps plant managers
The PayShepherd platform pulls in all the work orders, POs, contract rates and logic, union agreements, and site access data to provide maintenance and engineering managers a 360º understanding of services spend. Contractors use PayShepherd to submit costs, where they’re automatically validated against agreements and site access data to flag any invalid charges.
These invalid items can typically run 5% of the total cost or greater.
PayShepherd explains the reasons behind the invalid items to the contractors in real-time, so mill managers don’t have to wait for reconciliation or have uncomfortable conversations. It also provides visibility into rates for items that weren’t available (or present) previously, empowering more support from procurement to negotiate better deals.
Furthermore, PayShepherd reports daily contractor spending compared to PO/budget and accruals, allowing automatic daily submissions to accounting and finance. The platform also flags costs trending to an unplanned overage to allow dynamic scope adjustment to appease mill management and increase the likelihood of coming in under the planned budget.
All in all, PayShepherd reduces the administrative burden and pressures of superhuman expectations on maintenance and engineering managers. It empowers them to do what they do best and supports procurement, accounting, finance, and management in what they do best.